Linde adds robotic trucks to automation portfolio
9th March 2022
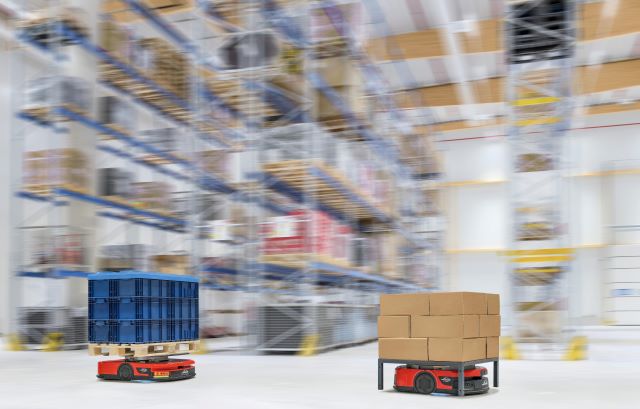
Autonomous transport vehicles open up great opportunities for even more efficient in-house logistics; with its Linde C-MATIC mobile robots, Linde Material Handling is expanding its extensive portfolio of automated solutions with three compact, agile and flexibly deployable logistics helpers for horizontal goods movements in warehouses and production.
Industrial robots that autonomously lift and move loads and navigate using QR codes have been in use for over a decade. But it is only now that many companies are discovering the benefits of these compact vehicles for their in-house material flow.
“Strong online commerce, on-going staff shortages, increasing goods movement in warehouses and production, and growing safety requirements to prevent personal injury and property damage have businesses looking for smart solutions to these challenges. Here the growing range of automated and autonomous systems comes in very handy for many companies,” says Philipp Stephan, Product Manager Automation & Intralogistics Solutions.
The new, compact and highly manoeuvrable Linde C-MATIC transport robots can handle maximum loads of 600, 1,000 and 1,500 kilograms even faster and with more agility. The “platforms on wheels”, which are around one meter long and just under one meter wide, can both turn on the spot and rotate the picked-up load. This means they require little space for driving or turning manoeuvres and are suitable for cramped warehouse layouts.
“The vehicles can be used in an extremely wide range of applications: They transport automotive components to modern production lines, they move building materials, spare parts, paper or clothing on pallets or in wire mesh crates through the warehouse, or bring ‘goods to people’, thus following a picking concept practiced primarily in online retailing,” says product expert Stephan, describing the situation.
Load pickup via table or pallet
The autonomous platform vehicles can pick up loads in two different ways: First, via a transport table that they can drive underneath, on which the goods, a pallet or a wire mesh crate are placed. Positioned underneath the table centre, a QR code ensures that the transported goods are not only picked up centrally and aligned correctly but can also be clearly identified. This means that the goods and their path through the facility can be tracked. Secondly, the transport robot can pick up the pallet directly or via a permanently mounted adapter plate from a transfer station or roller conveyor.
Goods handling is fully automatic: The Linde C-MATIC moves to a defined transfer point and places the surface of the load handling device centrally underneath the transport table or under the pallet positioned in a transfer rack. The cart then lifts the load and brings it to the designated staging area at a speed of up to 7.2km/h.
Navigation through the surrounding area is also accomplished via QR codes placed in a grid pattern on the floor and read by the QR camera installed on the vehicle. The transport robots receive information about the destination located at a short to medium distance from the warehouse management system, e.g. the “Linde Warehouse Navigator”. The vehicle’s software determines the optimal route through the building for each individual transport job.
A laser scanner ensures the reliable detection of moving or stationary obstacles. Thanks to real-time information processing, the Linde C-MATIC adapts its speed to the respective situation and remains stationary until people and vehicles have left the monitored zone. The vehicle automatically avoids fixed obstacles. It also issues visual and acoustic warning signals. Separate emergency stop switches on all four sides allow manual intervention. The mechanical shock absorbers fitted all around protect the vehicle from collision damage.
Wide variety of applications
The most common application is line transport between two points. But the transport robots can also interact with other autonomous or automated vehicles such as narrow-aisle trucks, reach trucks or pallet stackers by setting down or picking up goods at defined transfer points.
Charging of the lithium-ion battery is software-controlled: If the charge falls below a defined level or if there is currently no driving job to be carried out, the C-MATIC moves to the self-charging station and waits there for the next job.